As consumers and businesses require more control and detail in the manufacturing of products, and with industry demanding more precision and efficiency as well, the machines used to make the things we need increase in complexity by the day. But more often than we realize, it’s the simplest things that do the most, and this principle is what’s behind one of Foam Factory’s most exacting and efficient machines: the waterjet cutter.
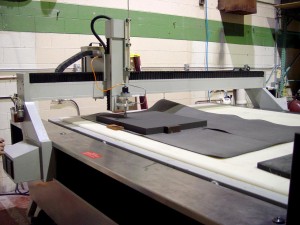
The original prototypes for water-pressure cutters were only able to produce short bursts of water, with far less pressure than machines are capable of today. Since then, the performance of these machines has increased to the point water pressures of 60,000 psi and greater are standard. Of course, the technology required to generate that kind of power is substantial, but the framework behind the first machines remains the same – the power of water can be used to break down even the most resilient materials.
There are two kinds of waterjet cutters; pure water cutting machines and machines that add abrasives to the water stream for extra cutting strength. Since the materials Foam Factory cuts are closed-cell foam and open-cell foam like polyurethane sponge foam, abrasives aren’t needed to make crisp cuts. However, the machine is compatible with abrasives, though the jobs and materials Foam Factory currently handles don’t necessitate the change. Industries that work with metal, wood, and exceptionally thick materials are more likely to take advantage of the extra cutting power abrasives provide.
Unlike many traditional saws and cutting machines used in foam fabrication, waterjet cutters can make cuts within the interior of a material without entering through exterior cuts. This is done by stopping the flow of water just like a faucet, moving the nozzle position to within the interior of the material, and turning the water back on to resume cutting. For things like foam gaskets or prototype concepts with an outer edge that needs to remain uncut, waterjet foam cutting is a smart choice.
Waterjet cutters run on computer programming, which eliminates the need for molds and plates that other cutting techniques require. But while this limits the practicality of large-scale jobs and projects, it makes short runs or single-item jobs like prototyping affordable and efficient, as it eliminates the cost and wait of die creation. When customers are able to provide data files for projects up front, small-run jobs can be produced in as little as an hour, from initial programming to the final cut being made. Producing the same project on a machine that requires dies and molds could take weeks.
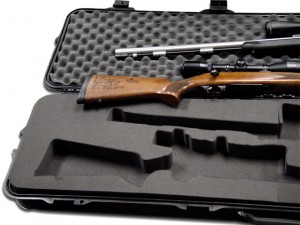
The speed with which waterjet computer cutting machines complete jobs is matched only by their precision. With non-abrasive cutters like Foam Factory’s, the diameter of the stream can be as thin as .005 of an inch. For perspective, a single sheet of standard 20LB copier paper is about .004 inches. This jet allows intricate angles and patterns, smooth curves, and perfectly straight lines to be cut with a degree of precision almost impossible to duplicate with the human hand. When considering the speed with which a waterjet machine is able to duplicate those designs multiple times over, there is no way even a team of individuals could match the machine’s capabilities. And with a 10 foot by 7 foot cutting surface, Foam Factory’s waterjet cutter can work on some of the largest sheets of foam for maximum efficiency.
Because of the nature of their foam sponge and foam rubber products, Foam Factory only runs their water jet at 45,000 psi, or about 75 percent of full power. 7 inch thick blocks of corrugated plastic are used to elevate and support sheets on the table. These blocks are small enough that they’re able to be flipped, rotated, and re-organized in different areas of the cutting table to maximize their life, since the power of the waterjet is more than enough to break down the plastic over time. Even with the reduction in pressure, if the machine were run 40 hours a week, the plastic support blocks would be rendered unusable in approximately one year.
So while technology is able to create fairly complex machination, like many things, the waterjet cutter is still based off one of the simplest ideas in nature – that water can erode and break down solids – reminding us that sometimes our newest technology can be rooted in the oldest ideas.